Thermal Runaway of Lithium Batteries
Thermal runaway in lithium batteries is indeed an inevitable phenomenon, primarily due to the highly reactive chemical nature of lithium metal, which demands extremely high environmental standards for its processing, storage, and use.
I. Causes of Lithium Battery Thermal Runaway
1. Internal Short Circuit:
When a short circuit occurs between the positive and negative electrodes inside the battery, it generates a large amount of heat, causing the battery temperature to rise rapidly and triggering thermal runaway. Short circuits may be caused by defects during battery manufacturing, diaphragm rupture due to battery aging, or dendrite growth piercing the diaphragm.
2. Overcharging:
When a battery is overcharged, the electrolyte inside undergoes decomposition reactions, producing a large amount of gas and heat, causing the battery temperature to rise rapidly and triggering thermal runaway. Overcharging may be caused by charger malfunctions, failure of the Battery Management System (BMS), or improper user operation.
3. External Damage:
When the battery is externally subjected to impact, compression, or puncture, the electrolyte inside leaks out and reacts chemically with oxygen in the air, producing a large amount of heat and gas, causing the battery temperature to rise rapidly and triggering thermal runaway.
4. Battery Aging:
As the battery usage time extends, the electrolyte inside gradually decomposes and ages, leading to a decrease in battery capacity, an increase in internal resistance, and a deterioration in heat dissipation performance, which can ultimately lead to thermal runaway.
5. High-Temperature Environment:
Lithium batteries operating in high-temperature environments for extended periods may cause the internal temperature to continue to rise, thereby triggering thermal runaway
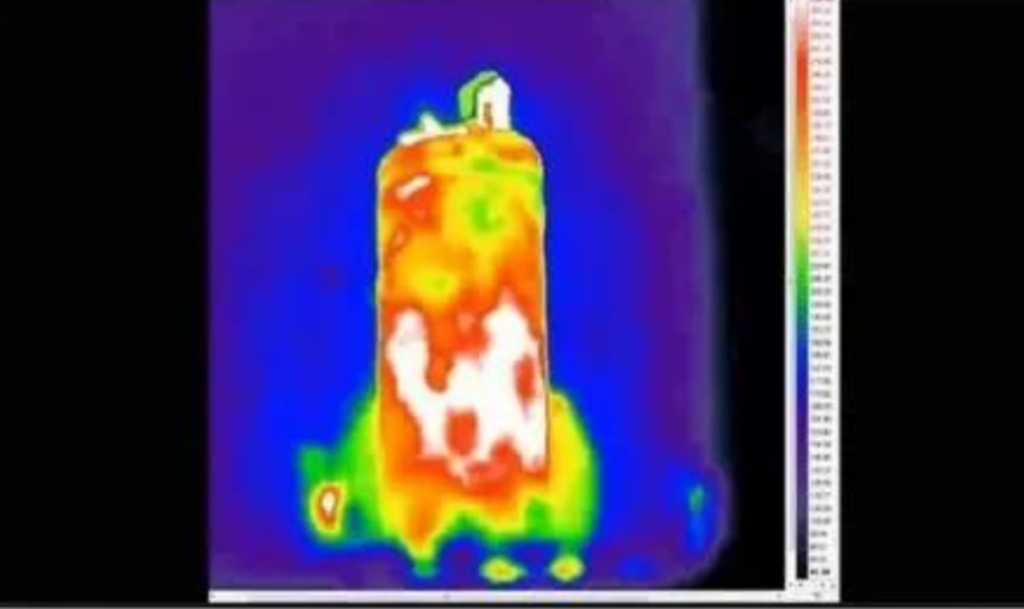
II. Response Measures for Lithium Battery Thermal Runaway
1. Improve Battery Manufacturing Precision:
In the production phase, strictly control the quality of electrodes and separators. Use high-precision cutting equipment to ensure electrodes are burr-free, and employ advanced quality inspection methods to guarantee the integrity and uniformity of separators.
2. Optimize Material Selection and Proportioning:
Choose stable positive and negative electrode materials and electrolytes. For positive electrode materials, prioritize thermally stable material systems while meeting energy density requirements. At the same time, select negative electrode materials capable of forming a stable SEI film, and reasonably adjust the composition of the electrolyte, adding some thermally stable additives to suppress the decomposition of the electrolyte.
3. Strengthen Battery Assembly Quality Control:
Establish strict assembly processes and standards, ensure accurate assembly of electrodes, separators, and other components through automated assembly equipment, and conduct strict sealing tests on assembled batteries.
4. Correct Charging and Discharging Methods:
Use chargers that meet the battery specifications to avoid overcharging and over-discharging. For lithium battery devices, set reasonable charging cut-off voltage and discharging cut-off voltage, and embed intelligent charging algorithms in device software or charging equipment to dynamically adjust charging current and voltage based on the battery’s condition.
5. Control the Use Environment Temperature:
Try to avoid using and storing batteries in high-temperature environments. If batteries are used in devices in high-temperature environments, install effective heat dissipation devices, such as heat sinks, fans, etc.
6. Regular Inspection and Maintenance:
For lithium battery devices in long-term use, regularly inspect the batteries, including visual inspections (for bulging, leakage, etc.) and performance tests (capacity, internal resistance, etc.).